How to Depin Automotive Connectors: Complete Removal Guide for Car Electrical Systems
Understand automotive connector dep inning
Define automotive connectors involve cautiously remove individual pins or terminals from their plastic housings without cause damage to either component. This essential skill prove invaluable for automotive technicians, DIY enthusiasts, and anyone work on vehicle electrical systems.
Modern vehicles contain hundreds of electrical connections, from simple lighting circuits to complex engine management systems. When repairs or modifications become necessary, know how to decent Devin connectors save time, money, and prevent costly mistakes.
Essential tools for connector dep inning
Success depend intemperately on use the right tools. Professional grade dep inning tools offer precision and reliability that makeshift alternatives can not match.
Primary dep inning tools
Dedicated dep inning tools, besides call terminal removal tools, come in various sizes to match different connector types. These tools feature just shape tips design to compress terminal retention tabs without damage surround components.
Pick sets provide versatility for different connector styles. Quality picks make from hardened steel resist bend and break during use. Avoid cheap plastic picks that may snap under pressure.
Needle nose pliers with fine tips help grasp and manipulate small terminals. Choose pliers with smooth jaws to prevent scratch or crush delicate components.
Support equipment
Good lighting eliminate guesswork and prevent mistakes. Lead work lights or magnifying lamps reveal fine details that overhead lighting might obscure.
Anti-static wrist straps protect sensitive electronic components from static discharge damage. While not invariably necessary for simple connectors, they provide insurance when work near expensive control modules.
Organize trays keep removing pins sorted and prevent loss. Smalcompartmentte containers work intimately for this purpose.
Connector types and identification
Automotive connectors come in numerous configurations, each require specific dep inning approaches. Understand these differences prevent damage and ensure successful removal.
Weather pack connectors
Weather pack connectors feature robust sealing and secure terminal retention. These connectors use a tang and slot system where terminals lock into position with spring load retention tabs.
The dep inning process require compress the retention tab while simultaneously pull the terminal from the rear of the connector. Weather pack terminals typically require moderate force for removal.
Metric pack connectors
Metric pack connectors offer high density connections in compact housings. These connectors use primary and secondary locking mechanisms for enhanced security.
Dep inningmetrici pack connectors oftentimes require remove secondarlocks’ks outset, so access individual terminal retention mechanisms. The compact design demand precision to avoid damage adjacent terminals.
Deutsch connectors
Deutsch connectors excel in harsh environments and high vibration applications. Their robust construction includes positive terminal retention and environmental sealing.
These connectors typically feature wedge type locks that require specific angles for successful dep inning. Understand the lock mechanism prevent excessive force application.
Step by step dep inning process
Successful dep inning follow a systematic approach that minimize risk and maximize efficiency. Rush through the process oftentimes lead to damage components and frustration.
Preparation phase
Begin by disconnect the connector from its mating half. Ne’er attempt to Devin connected assemblies, as this may damage both connectors and create safety hazards.
Examine the connector housing for secondary locks, keeper tabs, or other retention mechanisms. Many connectors feature multiple locking systems that must be address in proper sequence.
Identify the specific terminal require removal. Note its position and orientation for proper reinstallation belated.
Terminal access
Most automotive connectors allow terminal access from the wire side (rear )of the housing. Look for small slots or openings adjacent to each terminal position.
Some connectors require front side access, specially those with seal rear housings. These designs typically feature removable covers or access ports.

Source: YouTube.com
Clean any dirt or corrosion from access areas use appropriate solvents. Contamination can interfere with tool insertion and terminal movement.
Retention tab manipulation
Insert the appropriate dep inning tool into the access slot, feel for the terminal retention tab. These tabs vary in size, shape, and require compression force.
Apply steady pressure to compress the retention tab while simultaneously pull the terminal from the opposite end. Avoid excessive force that might break the tab or damage the terminal.
Some terminals require slight rotation during removal to clear housing features. Gentle manipulation commonly reveal the correct technique.
Terminal extraction
Once the retention tab releases, the terminal should slide freely from the housing. If resistance continue, stop and reassess the situation instead than force removal.
Grasp the terminal by its body or crimp area, ne’er by the wire lonely. Wire pull can damage the crimp connection and create future reliability problems.
Inspect the removed terminal for damage before set it by. Bent or damaged terminals may require replacement instead than reuse.
Common challenges and solutions
Flush experience technicians encounter difficulties during connector dep inning. Understand common problems and their solutions prevent frustration and component damage.
Stuck or corroded terminals
Corrosion can bond terminals to their housings, make removal highly difficult. Penetrate oils design for electrical components can help break these bonds.
Apply to penetrate oil slenderly to avoid contaminate other connections. Allow sufficient time for the oil to work before attempt removal.
Heat application sometimes help with stubborn terminals, but use caution to avoid melt plastic housings. Hair dryers provide gentle, control heat for this purpose.
Broken retention tabs
Excessive force or worn tools can break terminal retention tabs, compromise the connection’s security. Replacement terminals commonly provide the best long term solution.

Source: findpigtails.com
Some broken tabs can be repair use appropriate adhesives or mechanical methods, but these repairs may not meet original specifications.
Document any broken tabs for future reference, as these locations may require monitoring or eventual replacement.
Inaccessible terminals
Tight spaces and obstruct access complicate many dep inning operations. Remove surround components sometimes provide necessary clearance.
Angle or offset dep inning tools help reach terminals in confine spaces. These specialized tools justify their cost for frequent connector work.
Mirror inspection tools reveal hide retention mechanisms and access points that direct viewing can not show.
Safety considerations
Electrical work carry inherent risks that proper procedures can minimize. Safety consciousness protect both personnel and expensive vehicle systems.
Electrical safety
Disconnect the vehicle battery before begin extensive electrical work. This prevents accidental shorts and protects sensitive electronic components.
Verify power down status use appropriate test equipment. Some systems maintain power flush with the battery disconnect.
Use insulate tools when work near live circuits. Yet low voltage automotive systems can cause component damage or personal injury.
Component protection
Handle electronic control modules with appropriate anti-static precautions. Static discharge can cause immediate failure or latent damage that appear afterward.
Protect expose connectors from contamination during extended repair procedures. Plastic bags or cover prevent dirt and moisture intrusion.
Support heavy wire harnesses to prevent stress on remain connections. Zip ties or temporary supports distribute weight fitly.
Quality control and testing
Successful dep inning operations require verification to ensure proper completion and system integrity.
Visual inspection
Examine all remove terminals for damage, corrosion, or wear. Replace questionable components instead than risk future failures.
Check connector housings for cracks, broken tabs, or other damage that might affect performance. Minor damage may be repairable, but significant issues unremarkably require replacement.
Verify that all intend terminals were removed and none were unexpectedlydisturbedb during the process.
Electrical testing
Test remain circuits for continuity and proper operation before consider the job complete. Dep inning operations can sometimes affect adjacent connections.
Measure resistance values on critical circuits to ensure specifications remain within acceptable ranges.
Perform functional tests of affected systems when possible. This verification catch problems before the vehicle return to service.
Reinstallation best practices
Proper terminal reinstallation ensure reliable long term performance and prevent future problems.
Terminal preparation
Clean terminal surfaces use appropriate solvents to remove oils, dirt, and oxidation. Bright, clean surfaces provide optimal electrical contact.
Apply dielectric grease to terminals in harsh environments. This protection prevent corrosion and ensure reliable connections.
Inspect terminal retention features for damage that might prevent proper locking. Replace damage terminals before installation.
Installation technique
Insert terminal directly into their housings to avoid bind or cross threading. Misaligned installations can damage both terminals and housings.
Push terminals amply dwelling until retention tabs engage with audible clicks. Partial insertion create high resistance connections and potential failures.
Verify proper seating by mildly tug each terminal after installation. Decent install terminals should not move under moderate pulling force.
Troubleshoot connection problems
Understand common connection failures help diagnose problems and prevent recurrence.
Intermittent connections
Loose terminals cause intermittent operation that can be difficult to diagnose. These problems oftentimes worsen over time as vibration and thermal cycling increase wear.
Check terminal tension use appropriate gauges when available. Loose terminals may require replacement or careful adjustment.
Examine wire crimp connections for integrity. Poor crimps can cause intermittent problems that appear to be connector relate.
High resistance connections
Corrosion, contamination, or poor terminal contact create high resistance connections that affect system performance.
Measure voltage drop across suspect connections under load conditions. Excessive drops indicate connection problems require attention.
Clean and protect repair connections to prevent problem recurrence. Prevention costs less than repeat repairs.
Professional automotive electrical work demand attention to detail and proper technique. Master connector dep inning skills enable efficient repairs and modifications while maintain system reliability. Practice with common connector types build confidence and speed for more complex projects.
MORE FROM promospotlight.com
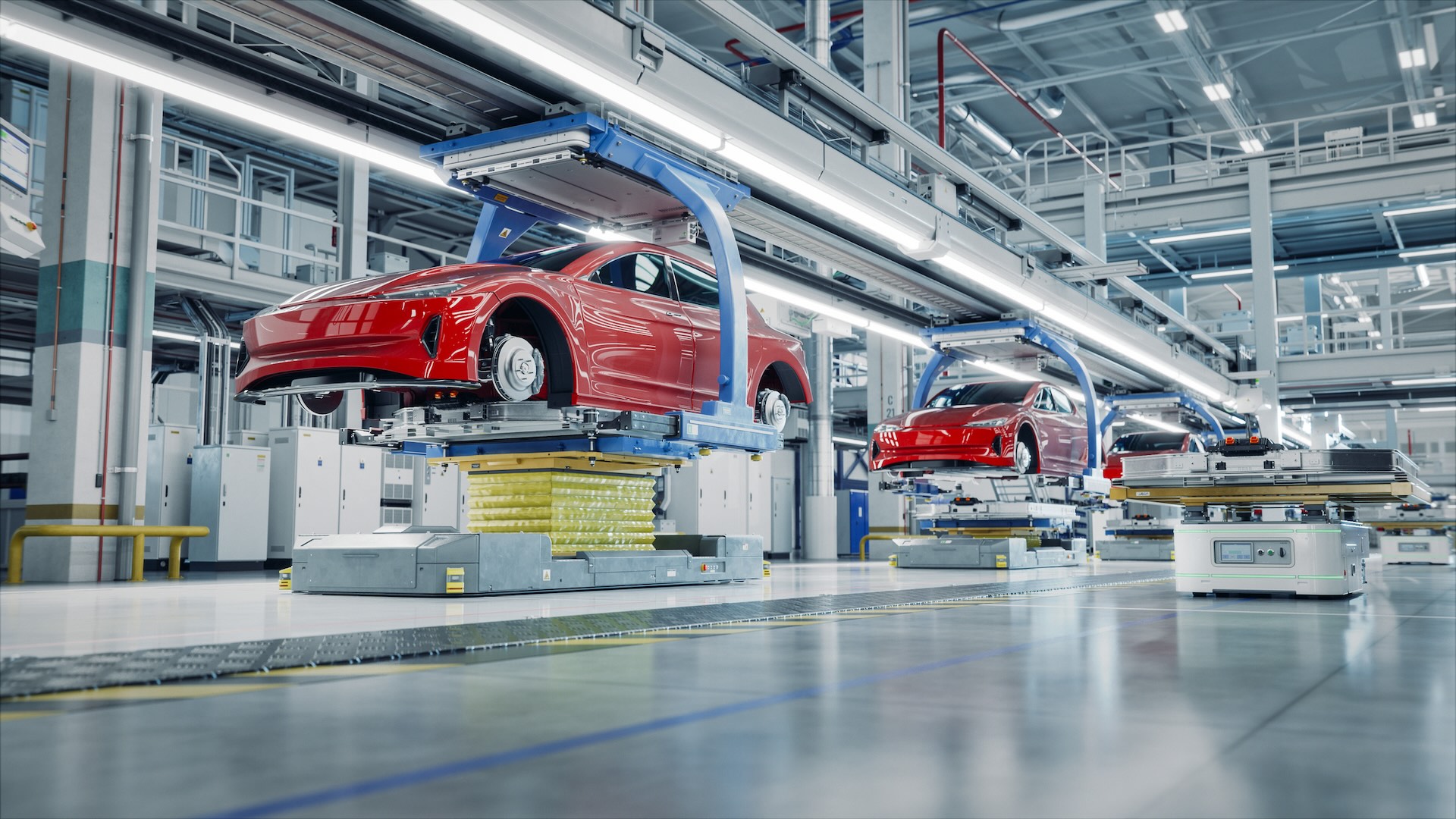
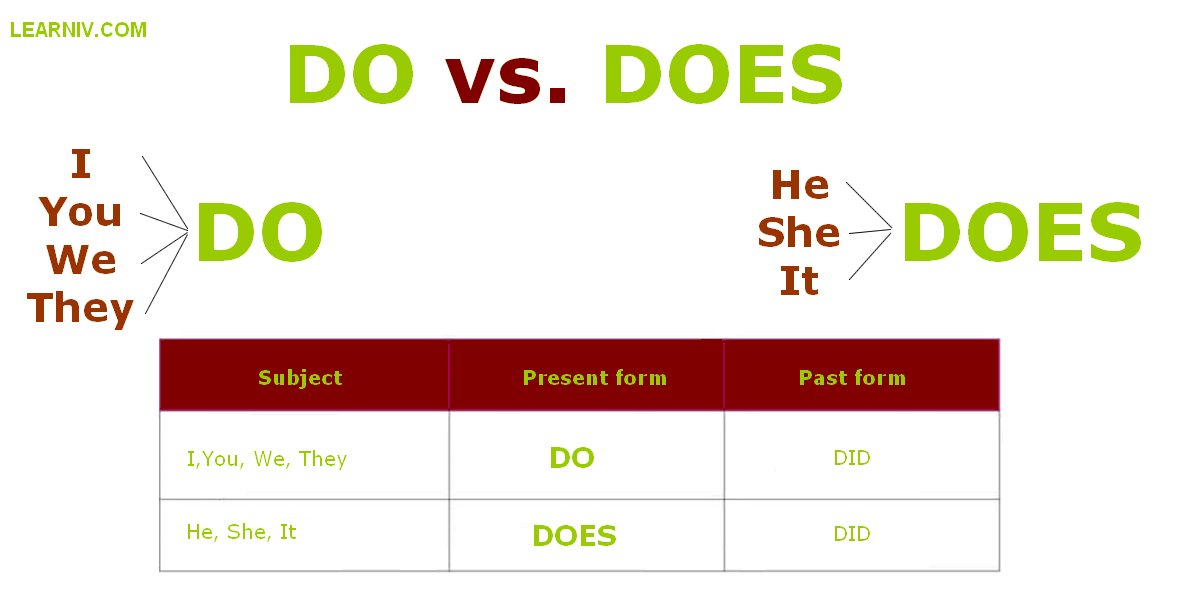
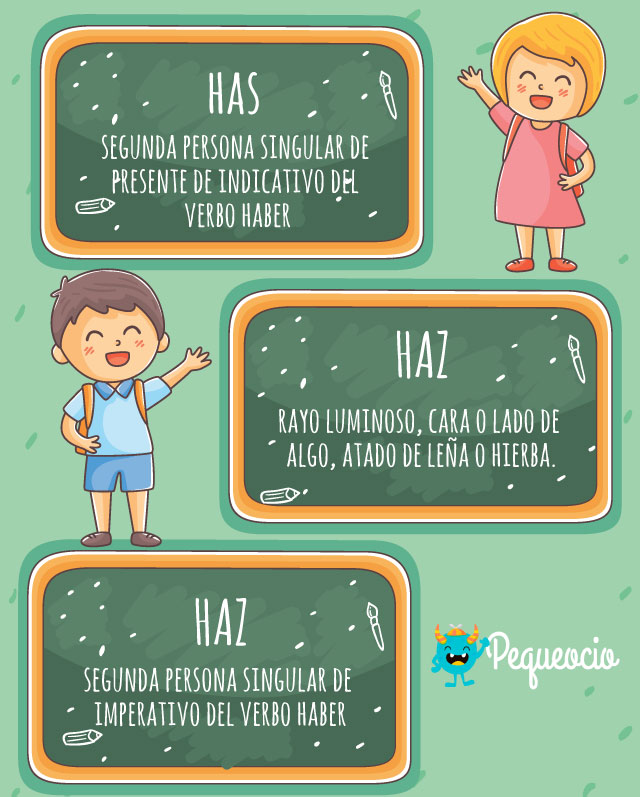
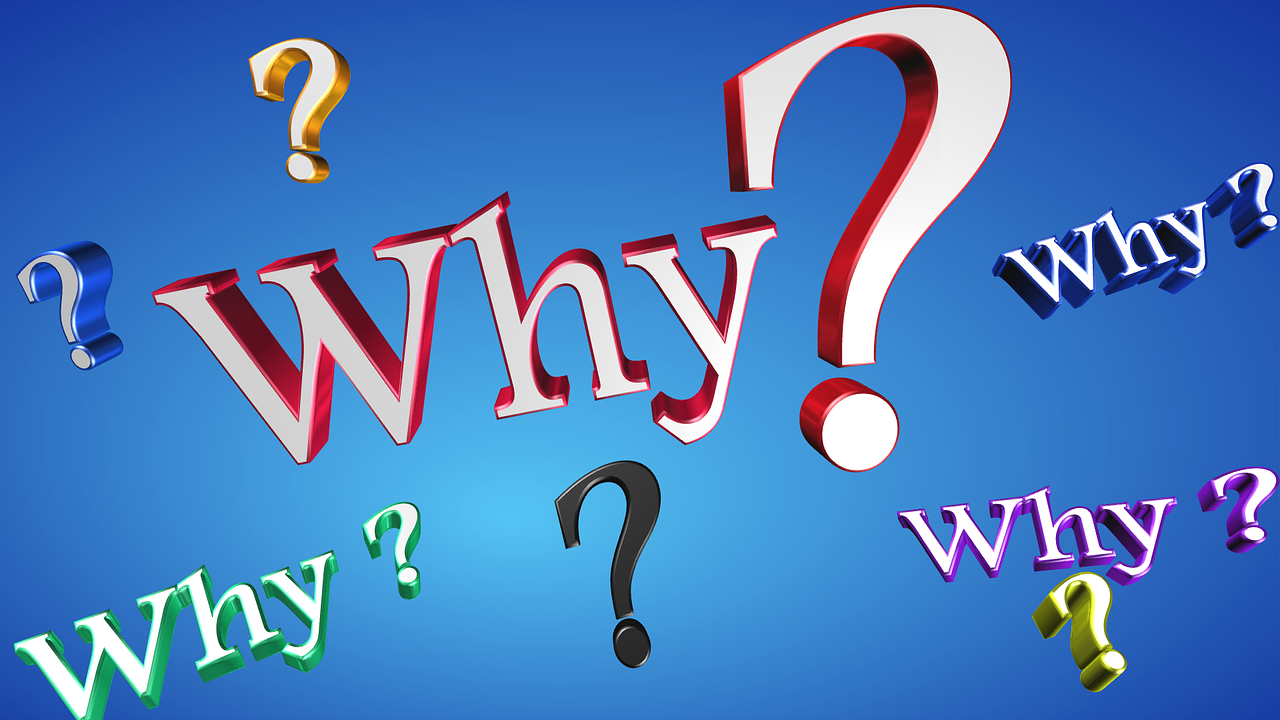
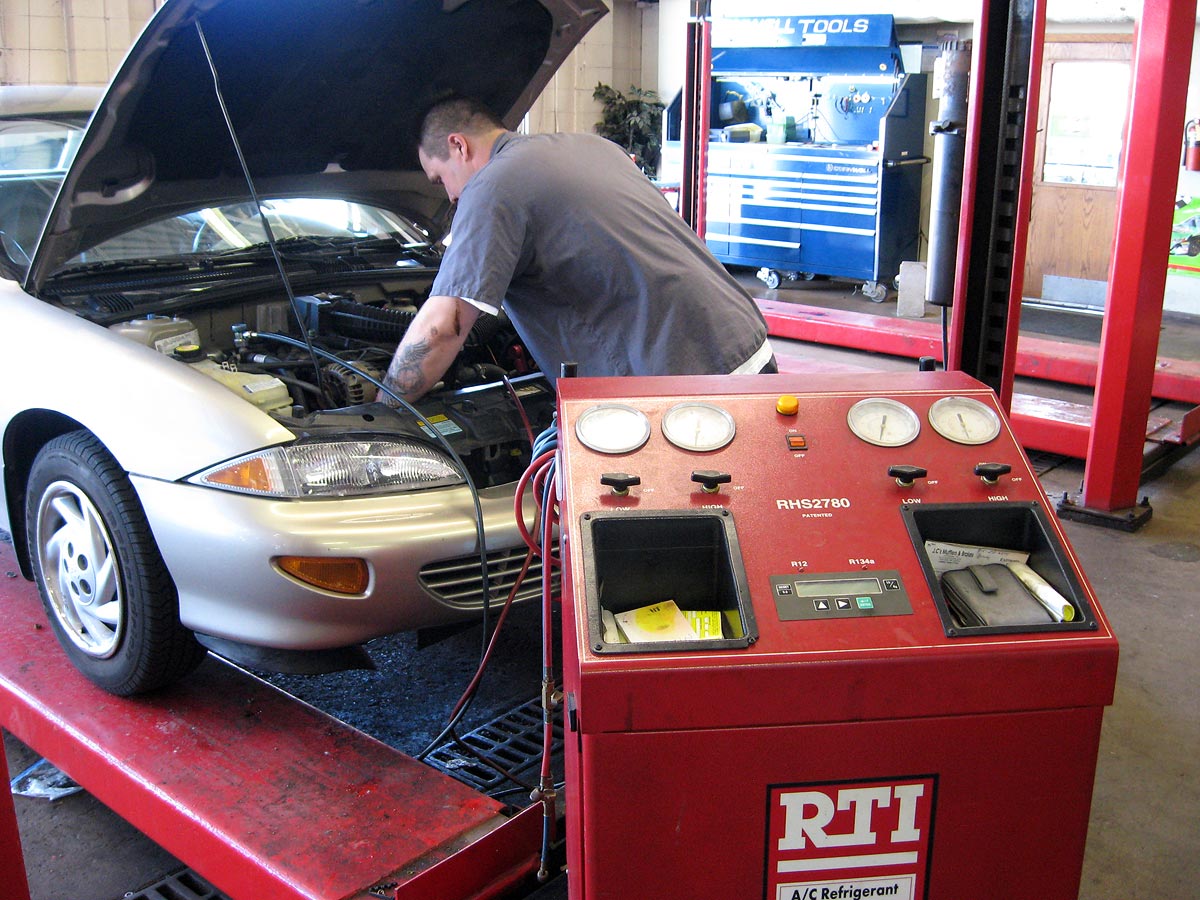
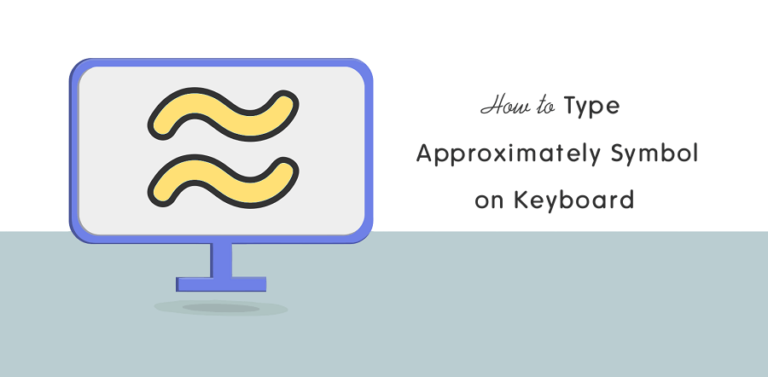
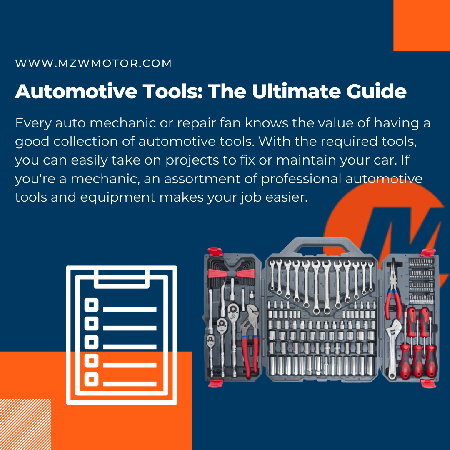
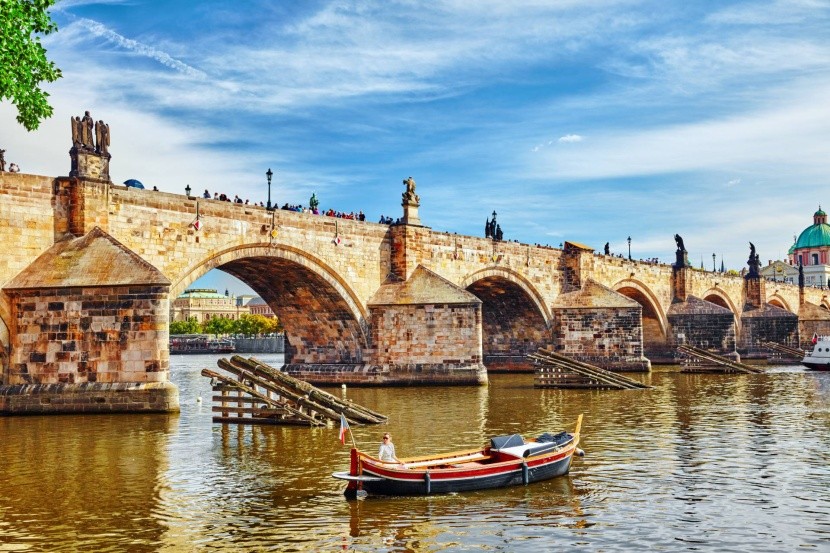
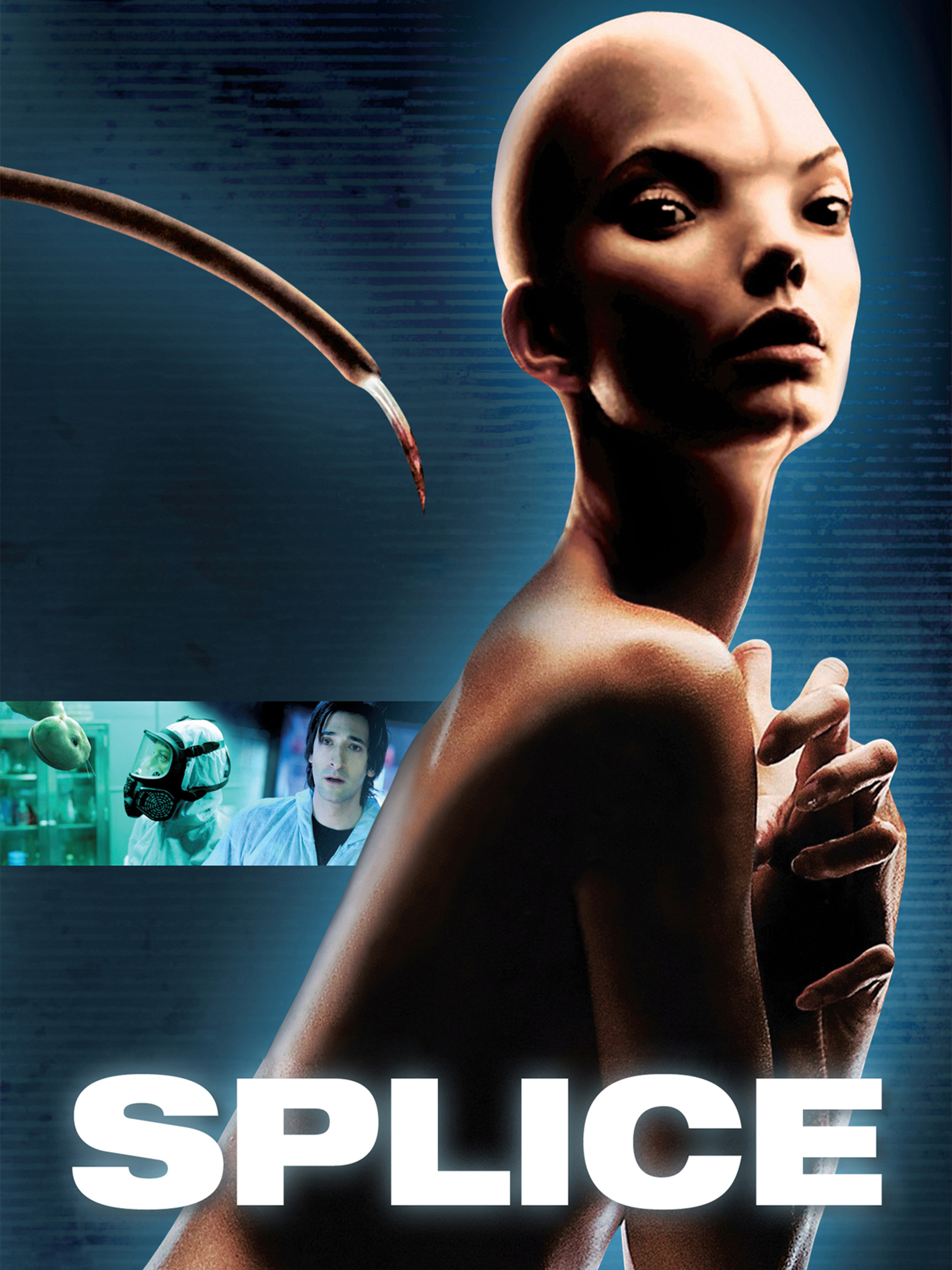
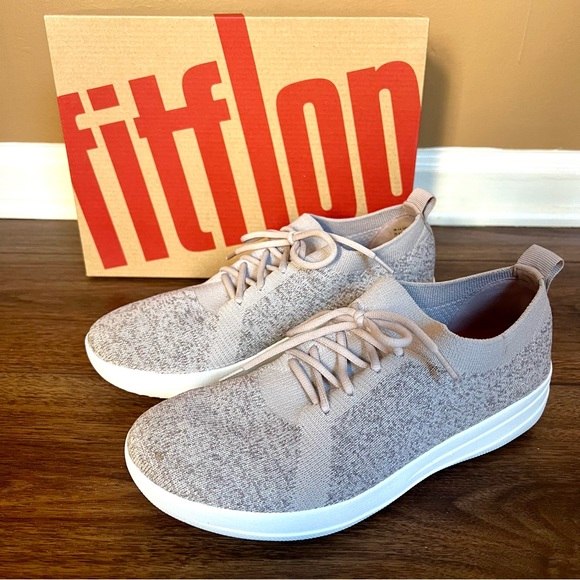
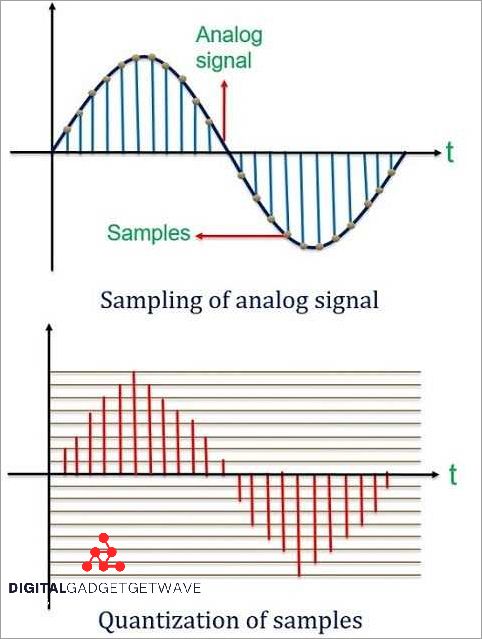
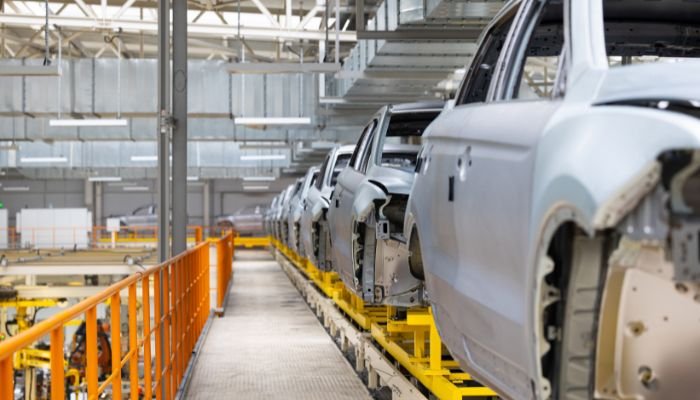