Automotive Sheet Metal: Understanding Thickness Standards and Applications
Understand automotive sheet metal thickness
Automotive sheet metal thickness vary importantly depend on the vehicle component, manufacturer specifications, and intend purpose. Most modern vehicles use sheet metal range from 0.020 inches (0.5 mm) to 0.060 inches (1.5 mm) thick. Yet, understand the complete picture require examine how manufacturers determine thickness requirements and how these measurements impact vehicle design, performance, and safety.
Common thickness measurements in automotive applications
Automotive manufacturers typically measure sheet metal thickness in either millimeters or gauge numbers. The gauge system can be confusing because higher gauge numbers indicate thinner metal. Here’s a breakdown of common automotive sheet metal thicknesses:
-
Body panels (doors, hood, trunk lid )
20 24 gauge (0.8mm 0.6 mm ) -
Structural components:
18 22 gauge (1.0mm 0.7 mm ) -
Frame rails:
14 16 gauge (1.9mm 1.5 mm ) -
Floor pans:
18 20 gauge (1.0mm 0.9 mm ) -
Roofs:
20 22 gauge (0.9mm 0.7 mm ) -
Fenders:
20 24 gauge (0.9mm 0.6 mm )
Luxury and high performance vehicles oftentimes use thinner sheet metal (higher gauge numbers )because they employ advanced high strength steel or aluminum alloys that provide rigidity despite reduced thickness.
Materials use in automotive sheet metal
The thickness requirements for automotive sheet metal vary base on the material use. Common materials include:
Mild steel
Traditional mild steel sheet metal typically require greater thickness to achieve necessary strength. Older vehicles from the 1950s 1980s oft use 18 gauge (1.0 mm )or thicker mild steel for body panels.
High strength steel (hHSS)
Modern vehicles progressively use high strength steel, which allow for thinner gauges while maintain or improve structural integrity. HSS components may range from 22 24 gauge (0.7mm 0.6 mm )while provide comparable strength to thicker mild steel.
Advanced high strength steel (aAHS))
AHS enable eventide thinner sheet metal applications, sometimes angstrom thin as 25 26 gauge ((.5mm 0.45 mm ))or certain body panels, while importantly improve crash performance and rigidity.

Source: cemjylgi.blob.core.windows.net
Aluminum
Aluminum body panels typically range from 0.8 mm to 1.2 mm in thickness. Though aluminum is less dense than steel, manufacturers oftentimes use slenderly thicker aluminum sheets to maintain appropriate stiffness and dent resistance.
Factors that determine sheet metal thickness
Automotive engineers consider multiple factors when determine the appropriate sheet metal thickness for various vehicle components:
Structural requirements
Components that contribute to the vehicle’s structural integrity require adequate thickness to withstand forces during normal operation and in crash scenarios. A pillars, b pillars, and frame rails typically use thicker sheet metal than exterior body panels.
Weight reduction goals
Manufacturers perpetually balance structural requirements against the need to reduce vehicle weight for improved fuel economy and performance. This has drive the trend toward thinner yet stronger sheet metal through advanced metallurgy and design techniques.
Manufacturing processes
The formability of sheet metal — its ability to be stamped, bent, and shape without crack or excessivspring backck — depend partially on thickness. Complex shapes may require specific thickness range to ensure successful manufacturing.

Source: whatispiping.com
Cost considerations
Thinner sheet metal typically cost less in raw materials, but may require more advanced alloys or additional reinforcement structures, create complex cost trade-offs that manufacturers must navigate.
Historical trends in automotive sheet metal thickness
Automotive sheet metal has undergone significant evolution over the decades:
1950s 1970s era
Vehicles from this period typically feature comparatively thick mild steel body panels, oft 18 20 gauge (1.0mm 0.9 mm ) These cars were knknownor their substantial feel but carry a significant weight penalty.
1980s 1990s transition
As fuel economy concerns grow, manufacturers begin reduce sheet metal thickness, sometimes to 20 22 gauge (0.9mm 0.7 mm ) while introduce galvanized coatings to prevent corrosion in these thinner panels.
Modern manufacturing
Contemporary vehicles use sophisticated computer modeling to optimize sheet metal thickness for each specific component. This has lead to variable thickness designs where a single panel might feature different thicknesses in different areas base on stress analysis.
Thickness variations by vehicle type
Different vehicle categories employ distinct approaches to sheet metal thickness:
Economy cars
Mass market vehicles oft use 22 24 gauge (0.7mm 0.6 mm )sheet metal for nonon-structuralody panels to minimize costs and weight. Yet, they rely on strategic reinforcements and crumple zones to maintain safety standards.
Luxury vehicles
Premium manufacturers oft use thinner sheet metal (sometimes 24 26 gauge or 0.6mm 0.5 mm )make from higher grade alloys. This approach reduce weight while provide the solid feel customers expect from luxury brands.
Trucks and SUVs
Utility vehicles typically employ thicker sheet metal, specially in load bear areas. Pickup truck beds might use 16 18 gauge (1.5mm 1.0 mm )steel to withstand heavy cargo and frequent impacts.
Performance cars
Sports cars ofttimes use aluminum or carbon fiber components with specialized thickness profiles optimize for weight reduction and rigidity. When steel is use, it’s typically high strength variants allow for thinner applications.
How thickness affects vehicle performance and safety
Sheet metal thickness flat impact several key vehicle characteristics:
Crash energy absorption
Decent design crumple zones rely on specific sheet metal thicknesses to deform predictably during collisions, absorb impact energy before it reach occupants. Also, thick or also thin, and these structures won’t will perform as will intend.
Noise, vibration, and harshness (nVH))
Thinner body panels can transmit more road and wind noise into the cabin. Manufacturers must balance thickness reduction against VH considerations, oftentimes add sound deaden materials to compensate for thinner metal.
Dent resistance
Thinner sheet metal is mostly more susceptible to dent from minor impacts like shopping carts or hail. Yet, advanced high strength steels and aluminum alloys can provide improved dent resistance flush at reduce thicknesses.
Longevity and corrosion
While thickness itself doesn’t inevitably determine corrosion resistance, thinner panels may perforate more promptly once corrosion begin. Modern coatings and galvanization help mitigate this concern.
After market and repair considerations
The thickness of automotive sheet metal have significant implications for vehicle repairs and modifications:
Repair challenge
Body shops must match the original sheet metal thickness when replace damage panels. Use thicker or thinner replacements can affect everything from panel alignment to crash performance.
Welding requirements
Different thicknesses require specific welding parameters. Modern ultra-thin high strength steels demand precise welding techniques to prevent burn through or inadequate penetration.
Custom fabrication
After market customizers typically use 18 20 gauge( 1.0mm 0.9 mm) mild steel for custom body panels, which is oft thicker than oOEMpanels. This pprovideseasier workability for hand form techniques but add weight.
Measure automotive sheet metal thickness
Several methods exist for determining the thickness of automotive sheet metal:
Ultrasonic thickness gauges
These non-destructive tools use sound waves to measure thickness without damage the panel. They’re specially useful for check exist vehicles without remove parts.
Micrometers
Traditional micrometers provide accurate measurements but require access to the edge of the sheet metal, make them more suitable for new materials than install panels.
Manufacturer specifications
Service manuals and manufacturer data sheets oftentimes list the specified thickness for replacement panels, provide valuable reference information for repairs.
Future trends in automotive sheet metal
The evolution of automotive sheet metal continue with several emerge trends:
Tailor weld blanks
This technology join sheets of different thicknesses before stamp, allow single components to have exactly optimized thickness in different areas base on structural requirements.
Ultra-high strength steel
New steel formulations with tensile strengths exceed 1000 MPA allow for regular thinner applications, sometimes below 0.5 mm while maintain structural integrity.
Multi material approaches
Kinda than focus exclusively on thickness, manufacturers progressively combine different materials — steel, aluminum, composites — to optimize weight, strength, and cost across the vehicle structure.
Conclusion
Automotive sheet metal thickness represent a complex balance of structural requirements, weight considerations, manufacturing constraints, and cost factors. While most modern vehicles use sheet metal range from 0.5 mm to 1.5 mm thick, the specific applications vary wide base on component function and material properties.
As automotive design will continue to will evolve, the trend toward will optimize, variable thickness components will use advanced materials will potential will accelerate. Understand these thickness standards help everyone from manufacturers to repair technicians ensure vehicles maintain their design performance and safety characteristics throughout their service life.
MORE FROM promospotlight.com
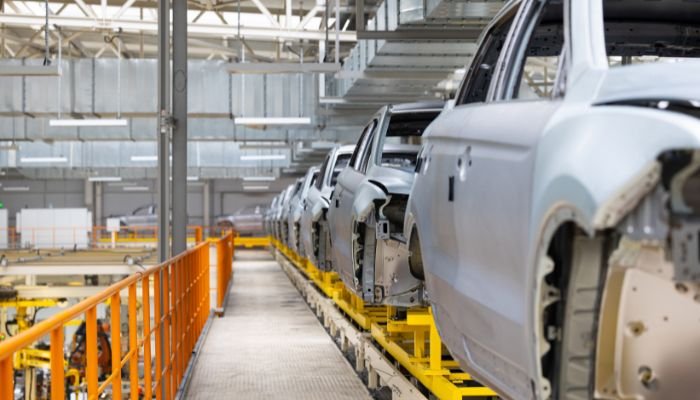
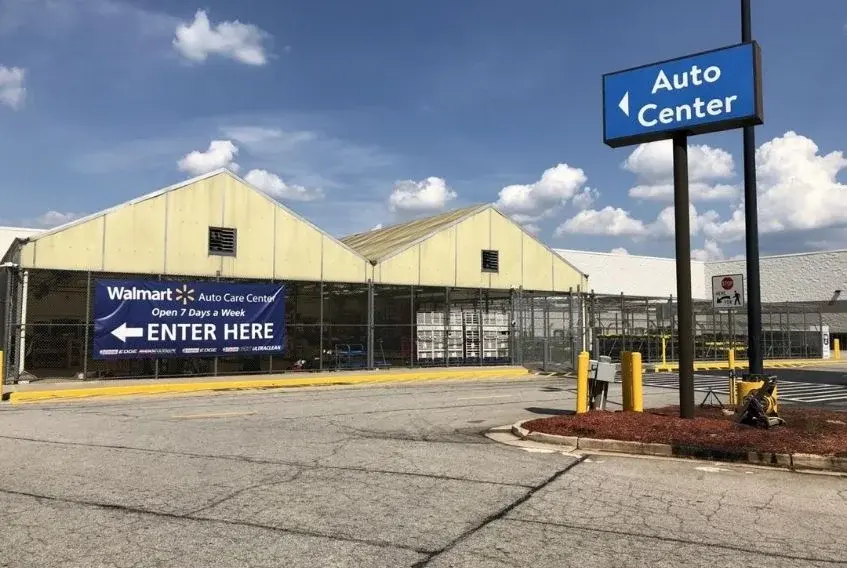
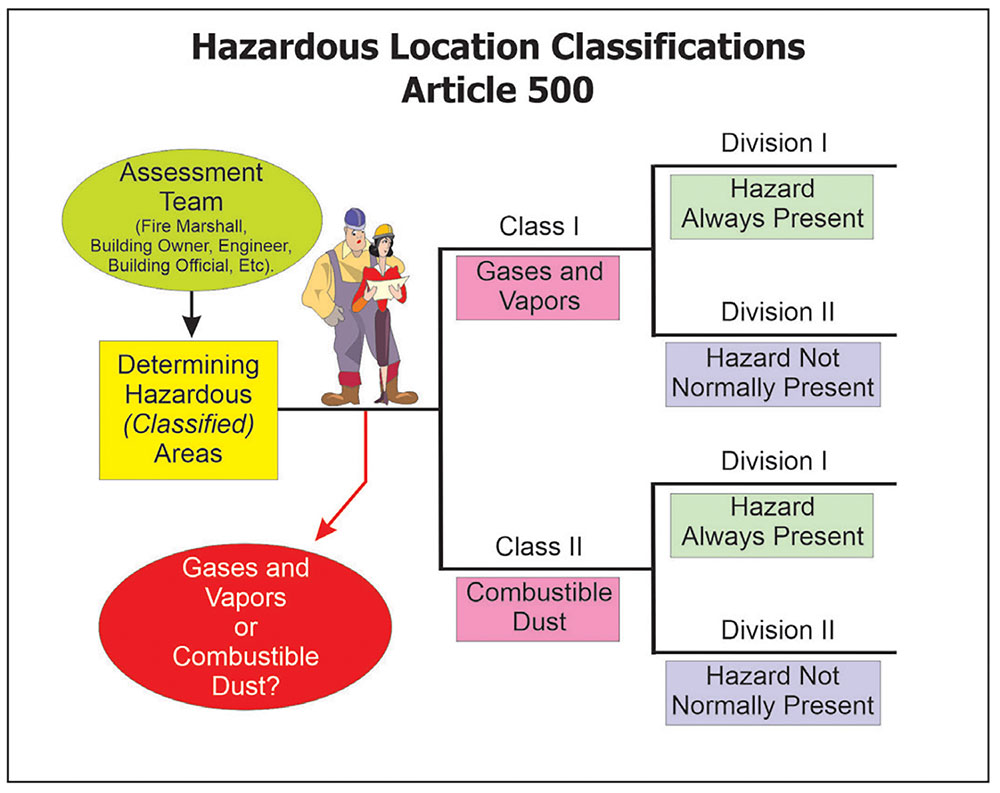
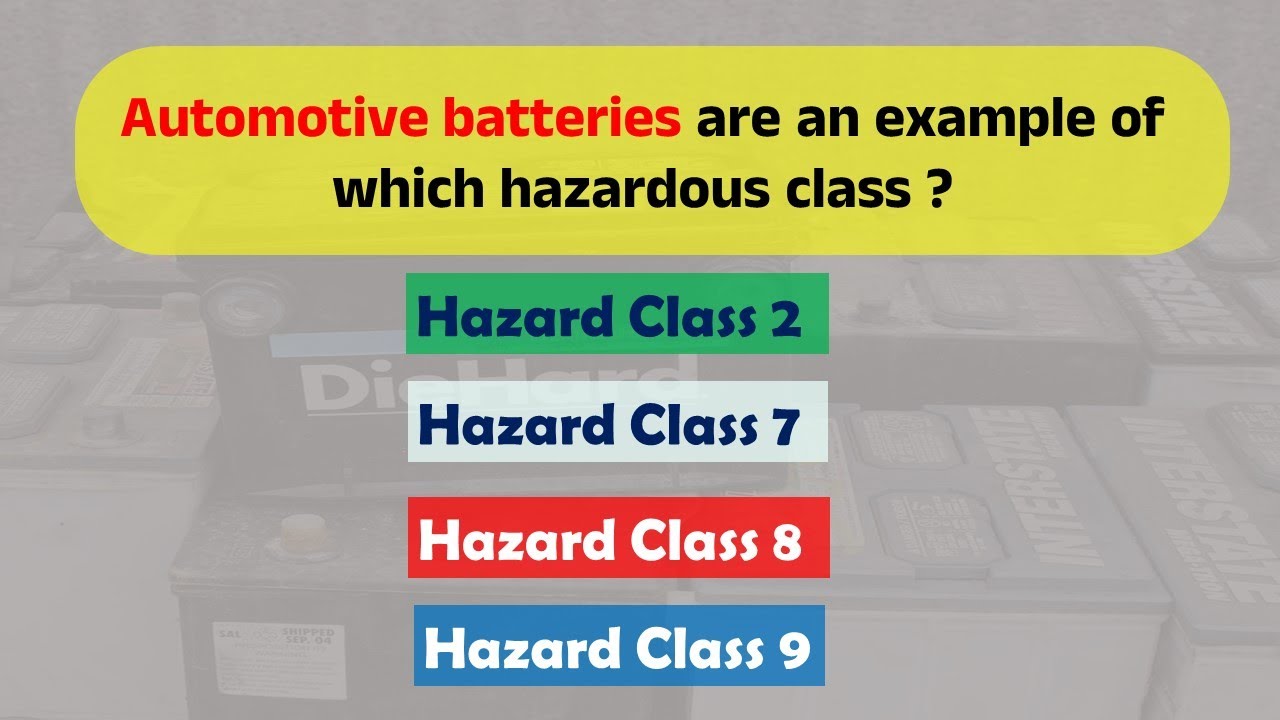
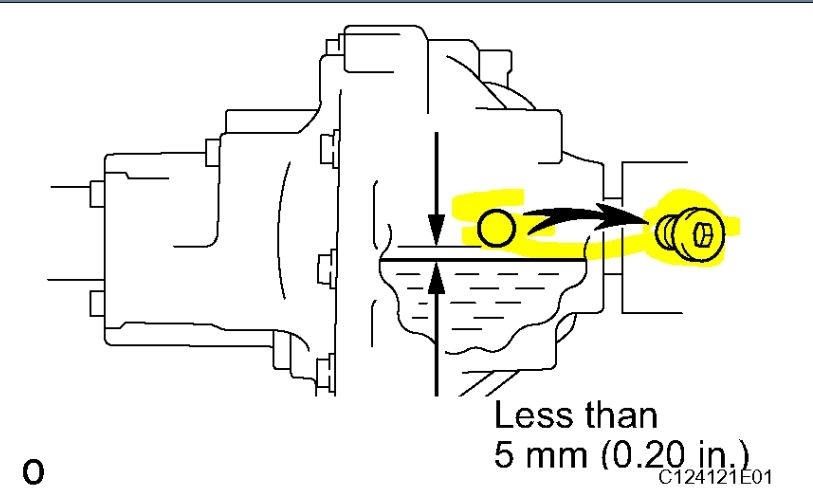
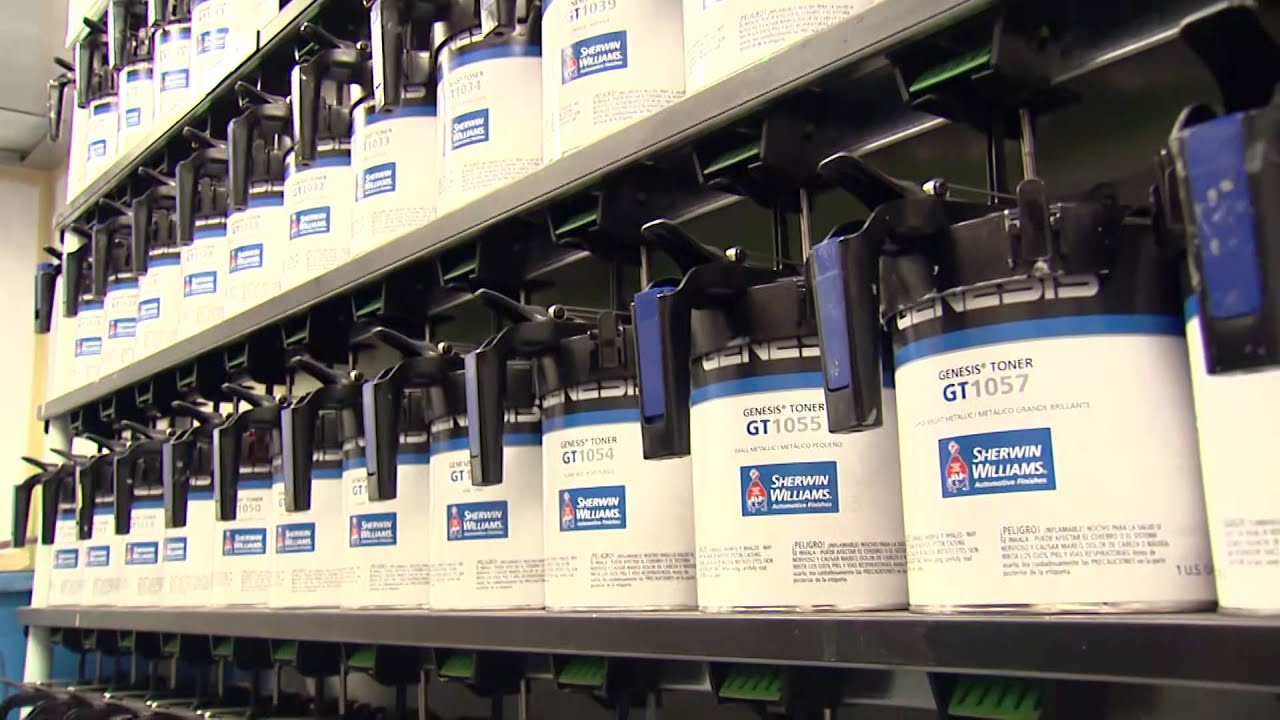
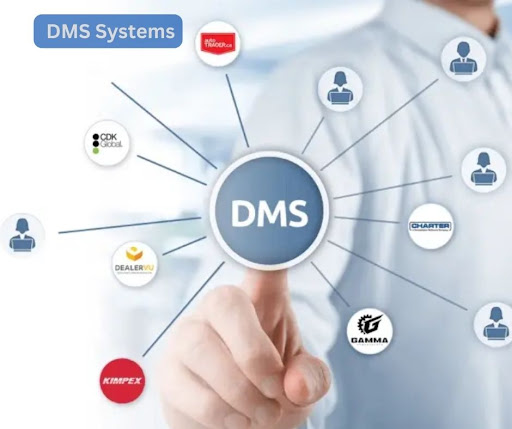
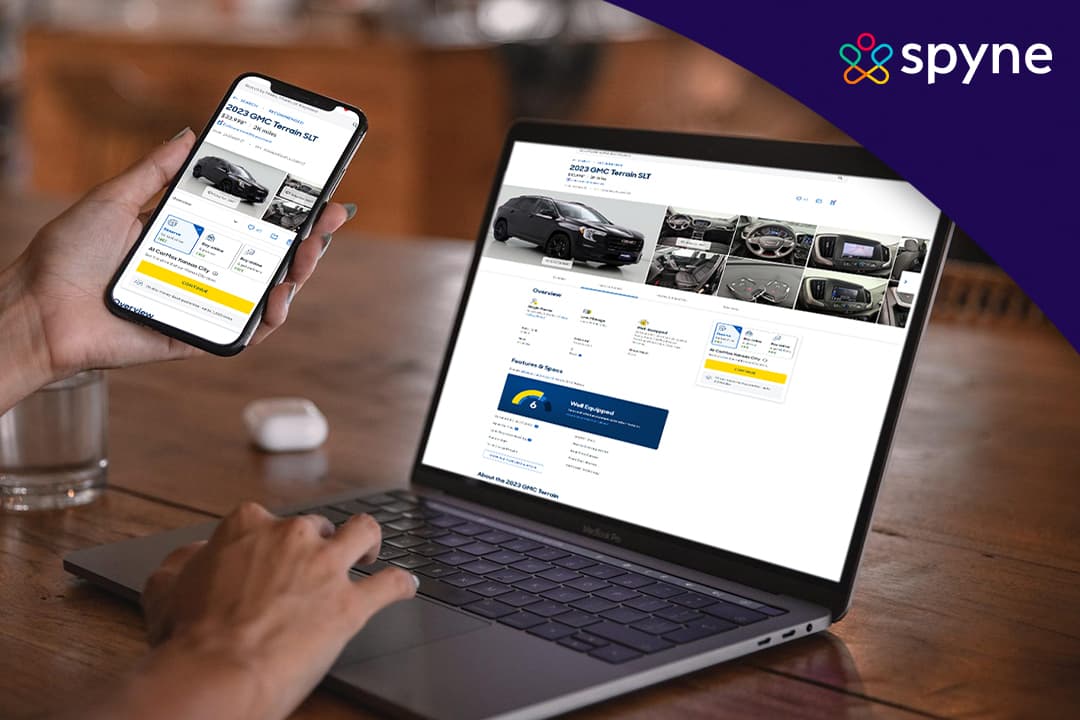
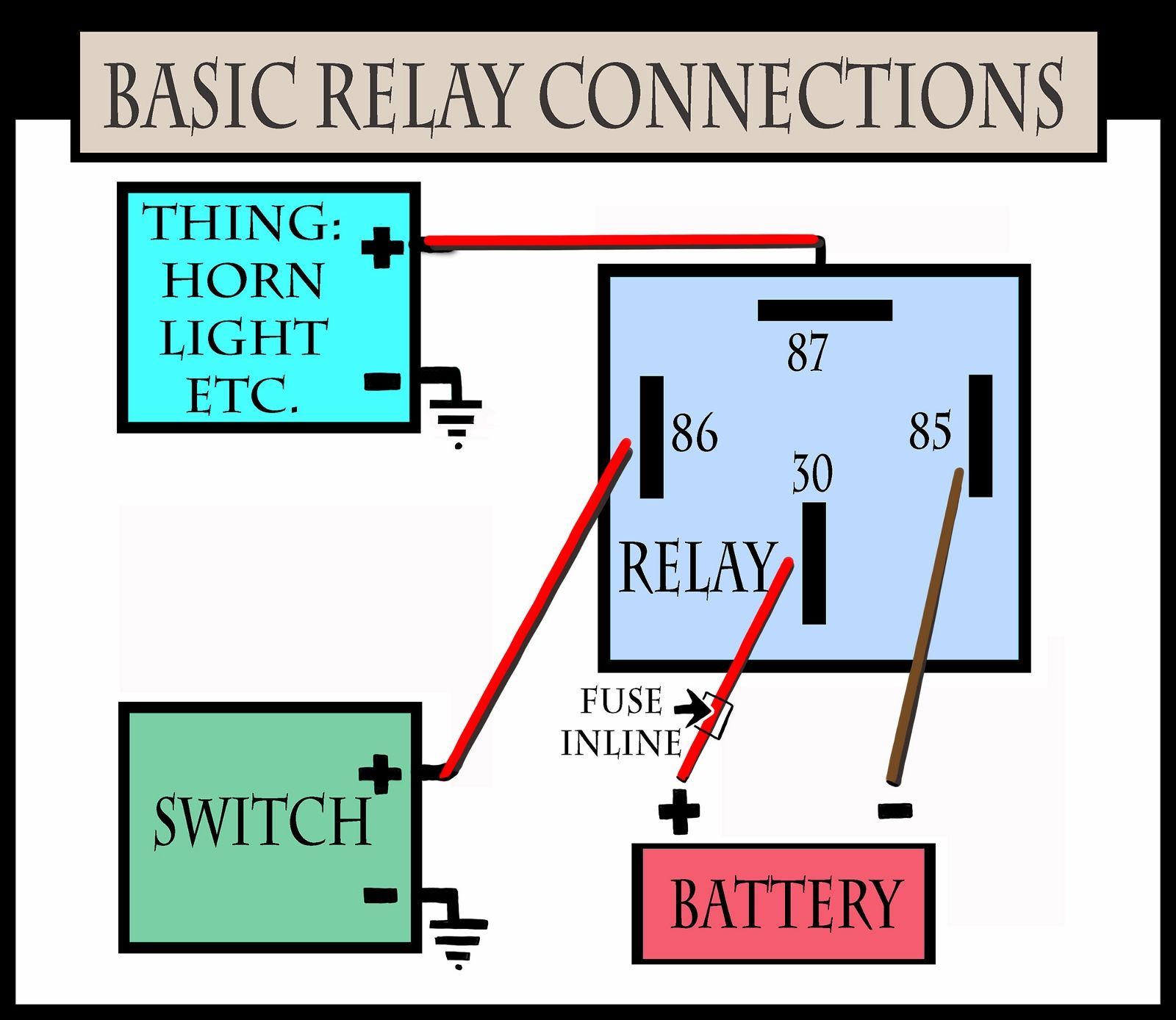
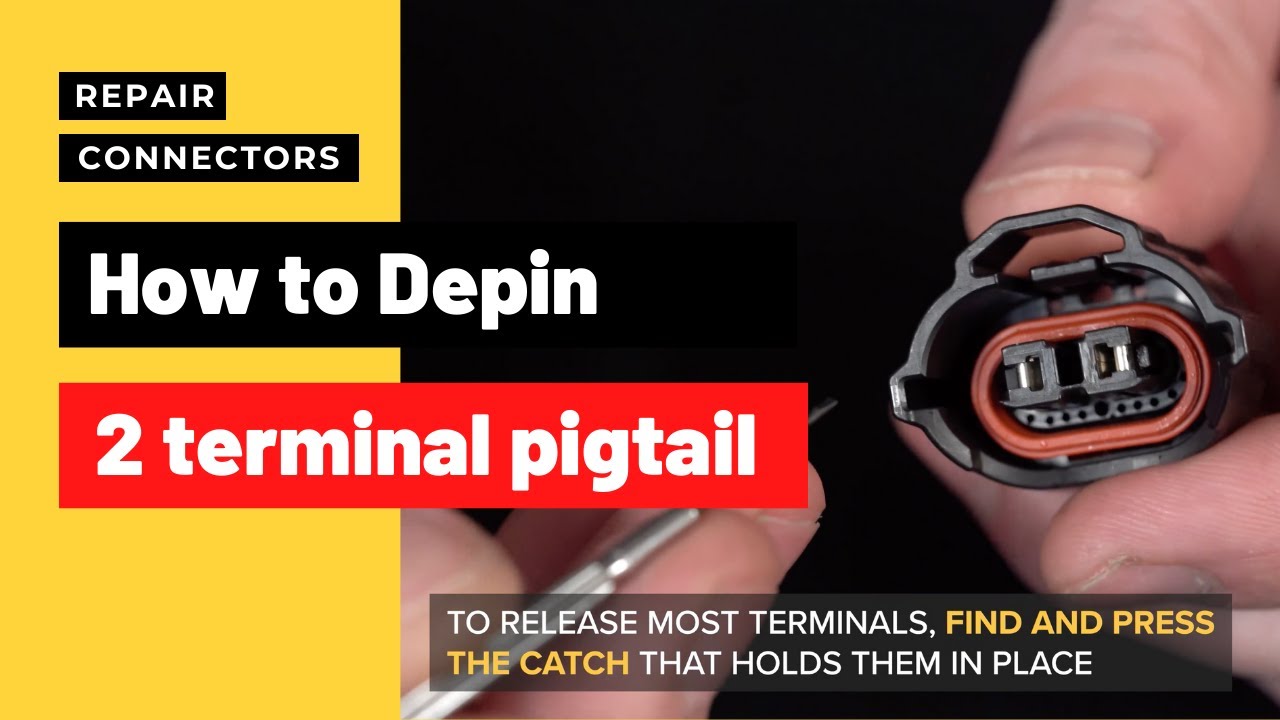
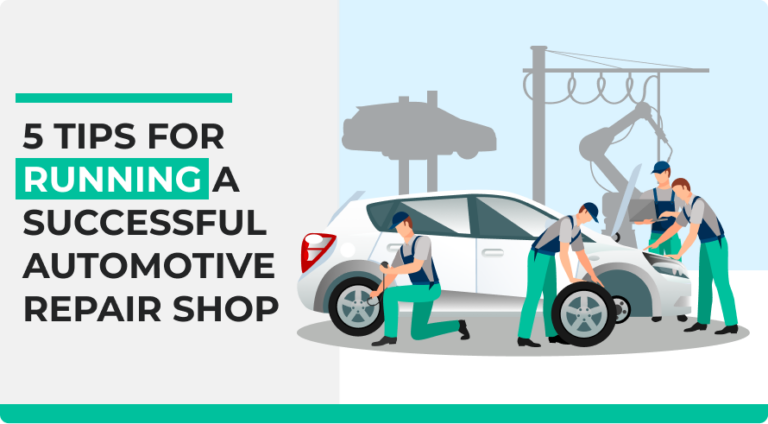
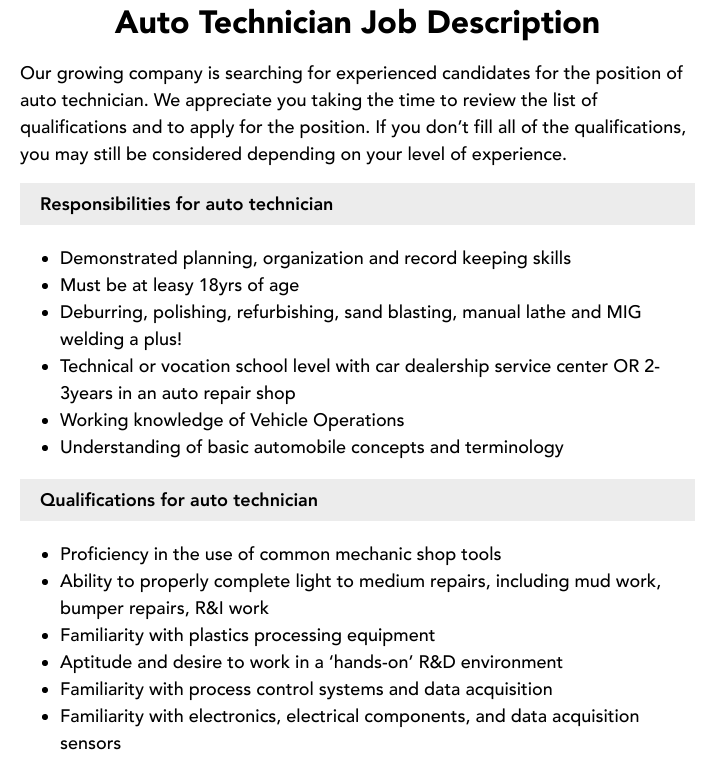