Automotive Battery Hazard Classification: Complete Safety Guide for Transportation and Storage
Understand automotive battery hazard classifications
Automotive batteries fall under specific hazard classifications that determine how they must be handled, transport, and store. The classification system ensure safety protocols are followed throughout the supply chain, from manufacture to disposal. Understand these classifications help mechanics, retailers, and consumers comply with regulations while maintain safety standards.
Primary hazard class for automotive batteries
Most automotive batteries are classified under Class 8 corrosive materials Accord to the department of transportation (dot )hazardous materials regulations. This classification apply specifically to wet cell batteries contain sulfuric acid electrolyte, which represent the majority of traditional automotive batteries presently in use.
The class 8 designation indicate that these batteries contain substances capable of cause severe damage to live tissue or materials through chemical action. Sulfuric acid, the primary electrolyte in lead acid automotive batteries, pose significant risks if handle improperly or if the battery casing become damage.
Lead acid battery specifications
Traditional lead acid automotive batteries contain roughly 35 % sulfuric acid by weight. This concentration level place them securely within the corrosive materials’ category. The acid serve as the electrolyte that enable the chemical reaction necessary for electrical energy storage and discharge.
These batteries besides contain lead plates and lead dioxide, which contribute to their hazardous nature. Lead is a toxic heavy metal that require special handling procedures to prevent environmental contamination and health risks.
Alternative battery types and their classifications
Modern automotive technology has introduced various battery types, each with distinct hazard classifications base on their chemical composition and construction.
Lithium-ion automotive batteries
Lithium-ion batteries use in electric and hybrid vehicles typically fall under Class 9 miscellaneous hazardous materials . These batteries present different risks compare to traditional lead acid units, include potential fire hazards and toxic gas emission under certain conditions.
The lithium-ion classification reflect concerns about thermal runaway, where batteries can overheat and potentially ignite. This risk require specialized packaging, handling, and transportation procedures that differ importantly from lead acid battery protocols.
Absorbed glass mat (aAGM)batteries
AGM batteries, while stock still contain sulfuric acid, may qualify for different transportation classifications depend on their construction. Some AGM batteries are classified anon-spillablele and may not require the same hazardoumaterials’ls documentation as traditional wet cell batteries.
The sealed construction of AGM batteries reduce the risk of acid spill during normal handling and transportation. Nonetheless, they however contain corrosive materials and require appropriate safety precautions.

Source: energylast.com
Transportation regulations and requirements
Ship automotive batteries require compliance with multiple regulatory frameworks, include dot regulations for domestic transport and international air transport association (iIATA)rules for air shipment.
Proper shipping names and documentation
When ship automotive batteries, the proper shipping name must appear on all documentation. For wet cell batteries, the designation is typically” battery, wet, fill with acid, electric storage. ” tThisspecific terminology ensure proper handling throughout the transportation process.
Shipping documentation must include the hazard class, identification number, and proper shipping name. These requirements help transportation personnel understand the risks and apply appropriate safety measures.
Packaging requirements
Automotive batteries require specific packaging standards to prevent damage and contain potential spills. Packaging must be design to withstand normal transportation stresses while maintain the integrity of the battery casing.
Individual batteries typically require cushioning material and leakproof containers. Multiple batteries must be separate to prevent short circuits and secure to prevent movement during transport.
Storage and handling safety protocols
Proper storage of automotive batteries involve understand their hazard classification and implement appropriate safety measures. Storage areas must provide adequate ventilation to prevent hydrogen gas accumulation and maintain appropriate temperature ranges.
Ventilation requirements
Battery storage areas require mechanical or natural ventilation to disperse hydrogen gas that may be release during charge or normal operation. Hydrogen is extremely flammable and can create explosive conditions in confine spaces.
Ventilation systems should provide air changes sufficient to maintain hydrogen concentrations advantageously below the lower explosive limit. This typically require continuous air movement and monitoring in commercial storage facilities.
Spill response procedures
The corrosive nature of automotive batteries necessitate specific spill response procedures. Personnel must have access to appropriate neutralize agents, typically sodium bicarbonate or commercial acid neutralizers.
Emergency equipment should include acid-resistant gloves, eye protection, and respiratory protection. Spill kits must be pronto available in areas where batteries are store or service.
Workplace safety considerations
Automotive service facilities and battery retailers must implement safety programs that address the specific hazards associate with battery handling. These programs should include employee training, personal protective equipment requirements, and emergency response procedures.

Source: storage.googleapis.com
Personal protective equipment
Workers handle automotive batteries require appropriate personal protective equipment base on the corrosive hazard classification. This includes chemical resistant gloves, safety glasses or face shields, and protective clothing that can withstand acid contact.
Respiratory protection may be necessary in unwell ventilate areas or when handle damage batteries that may release acid vapors. The specific requirements depend on the workplace assessment and potential exposure levels.
Training requirements
Employee training programs must address the specific hazards associate with automotive batteries, include the corrosive nature of the electrolyte and proper handling procedures. Training should cover normal handling procedures ampere advantageously as emergency response protocols.
Regular refresher training ensure that employees remain current with safety procedures and regulatory requirements. Documentation of training completion is typically required for regulatory compliance.
Environmental considerations and disposal
The hazard classification of automotive batteries extend to their disposal and recycling. Lead acid batteries are considered hazardous waste and require proper disposal through authorized recycling facilities.
Recycling requirements
Automotive batteries contain valuable materials that can be recovered through recycling processes. Lead, plastic, and acid can all breclaimedim and reuse in new battery production. Nonetheless, the hazardous nature of these materials require specialized handling throughout the recycling process.
Many jurisdictions require battery retailers to accept use batteries for recycling. This help ensures proper disposal and prevent environmental contamination from improper disposal practices.
Environmental impact
Improper disposal of automotive batteries can result in soil and groundwater contamination due to their corrosive and toxic components. Lead contamination pose particular risks to human health and environmental systems.
Regulatory frameworks govern battery disposal reflect their hazard classification and the potential for environmental damage. Compliance with these regulations protect both human health and environmental resources.
Regulatory compliance and best practices
Maintain compliance with automotive battery hazard classifications require understand multiple regulatory frameworks and implement comprehensive safety programs. Organizations handle these batteries must stay current with regulatory changes and industry best practices.
Documentation and record keeping
Proper documentation of battery handling, storage, and disposal activities support regulatory compliance and provide evidence of safety program implementation. Records should include training documentation, inspection reports, and incident reports.
Shipping records must accurately reflect the hazard classification and comply with transportation regulations. This documentation follow the batteries throughout the supply chain and ensure proper handling at each stage.
Regular safety audits
Periodic safety audits help identify potential compliance issues and opportunities for improvement. These audits should evaluate all aspects of battery handling, from receipt and storage to disposal and recycling.
Audit findings should be document and address quickly to maintain compliance and ensure worker safety. Regular audits demonstrate commitment to safety and regulatory compliance.
Understand automotive battery hazard classifications is essential for anyone involve in their manufacture, distribution, sale, or service. The class 8 corrosive materials’ designation for traditional lead acid batteries reflect the serious safety considerations require throughout their lifecycle. Proper compliance with these classifications protect workers, consumers, and the environment while ensureto continuee safe use of these essential automotive components.
MORE FROM promospotlight.com
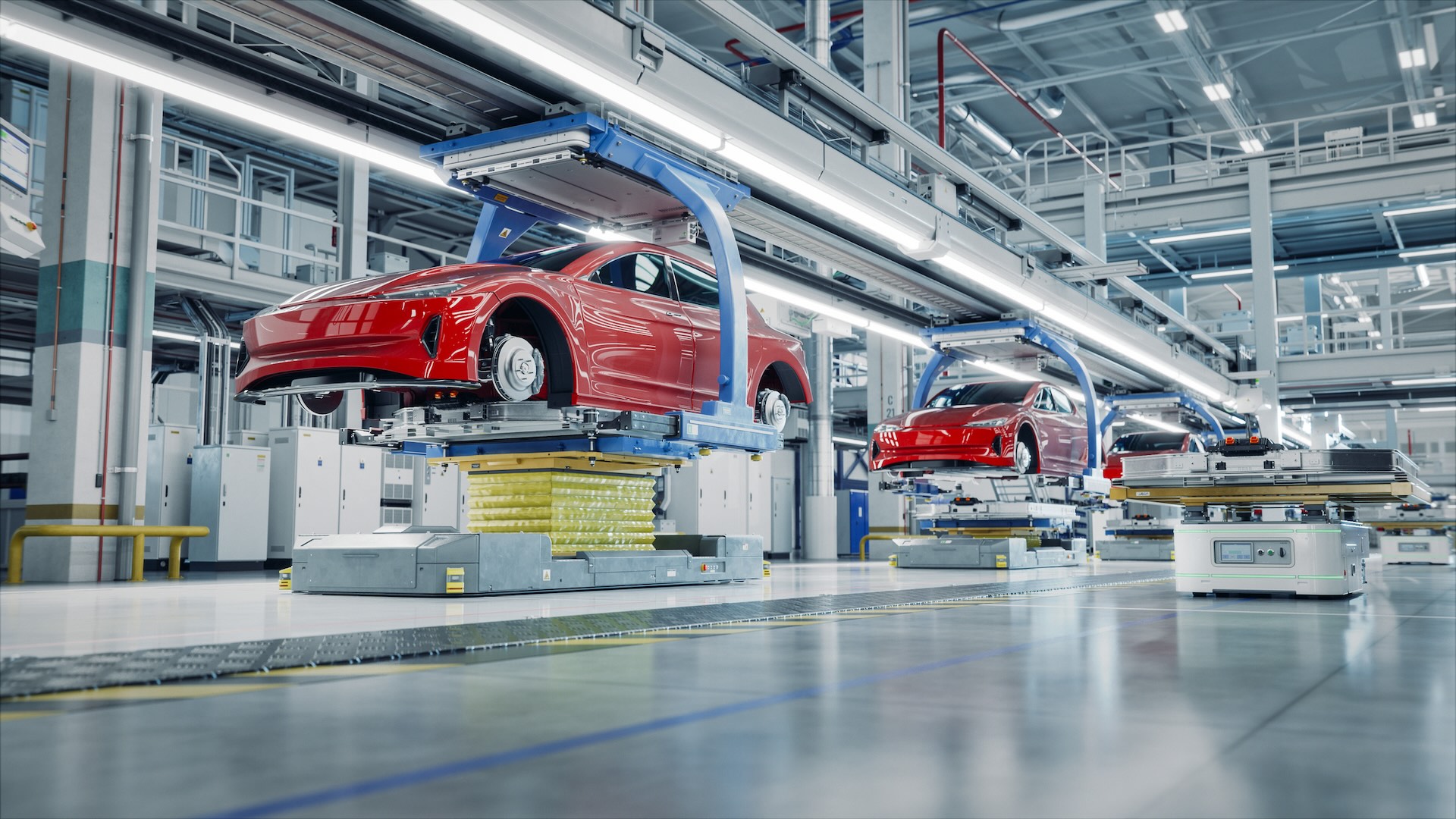
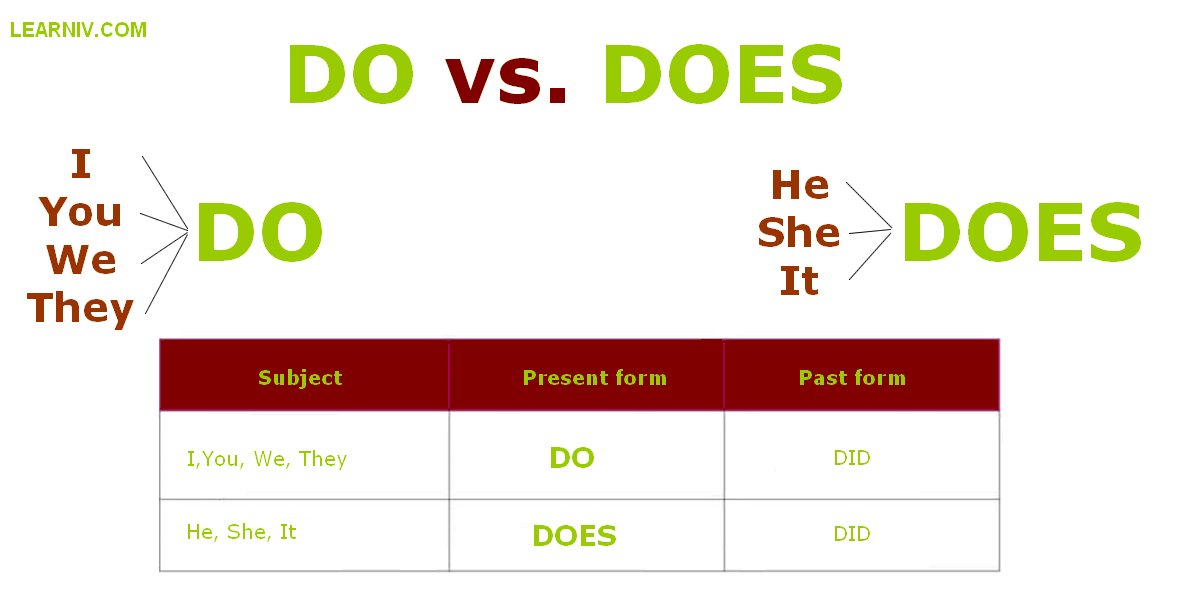
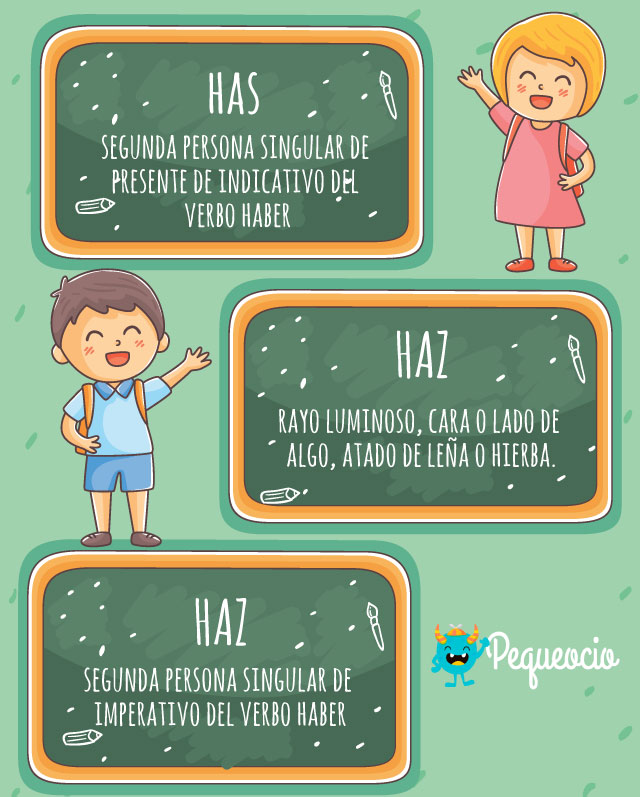
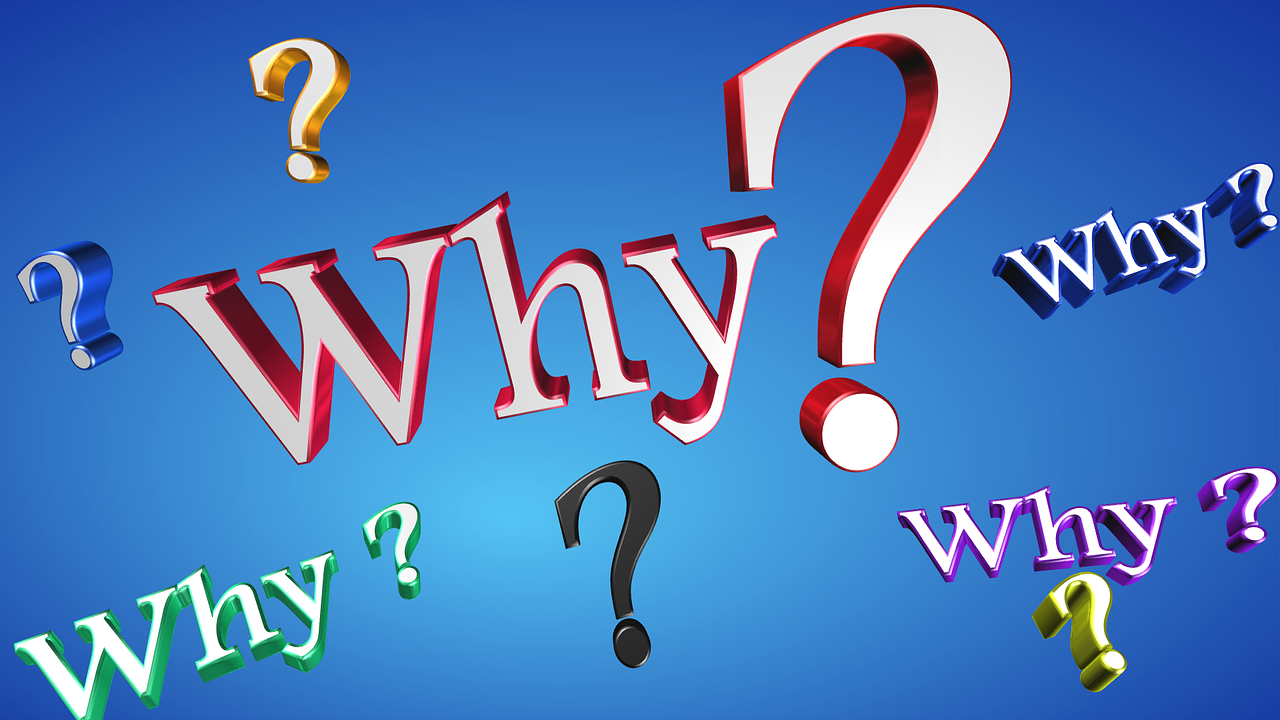
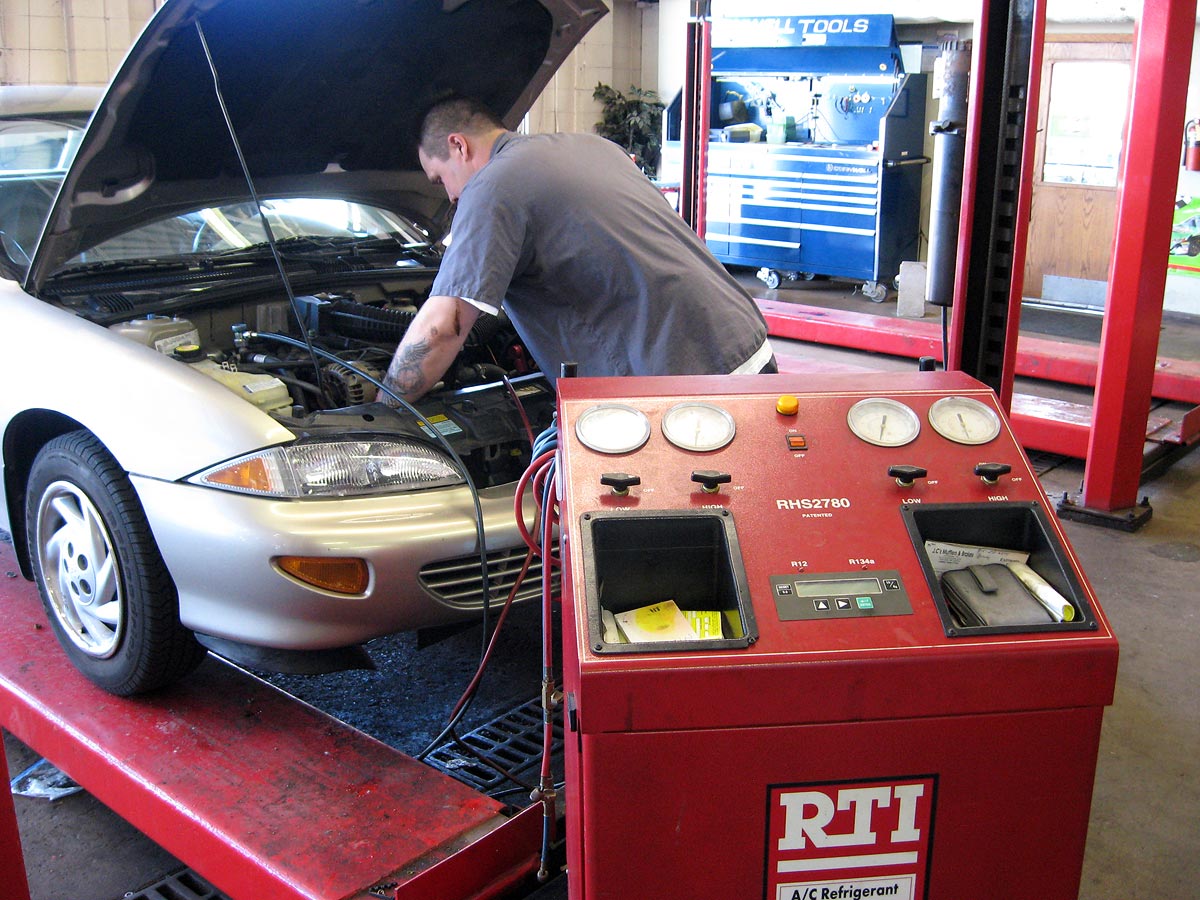
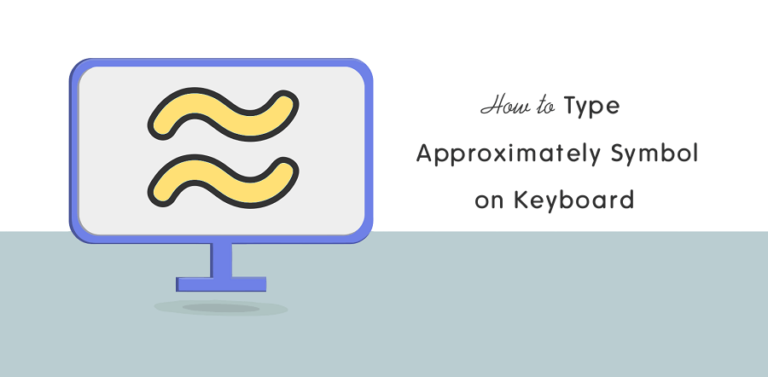
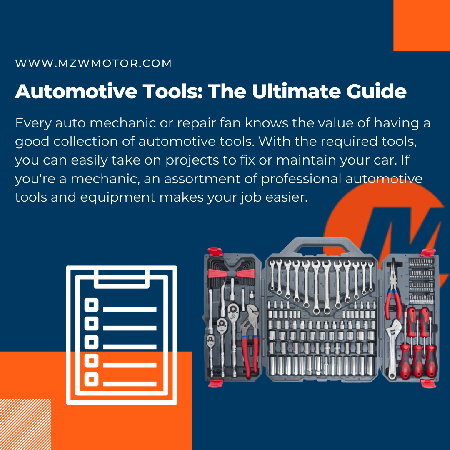
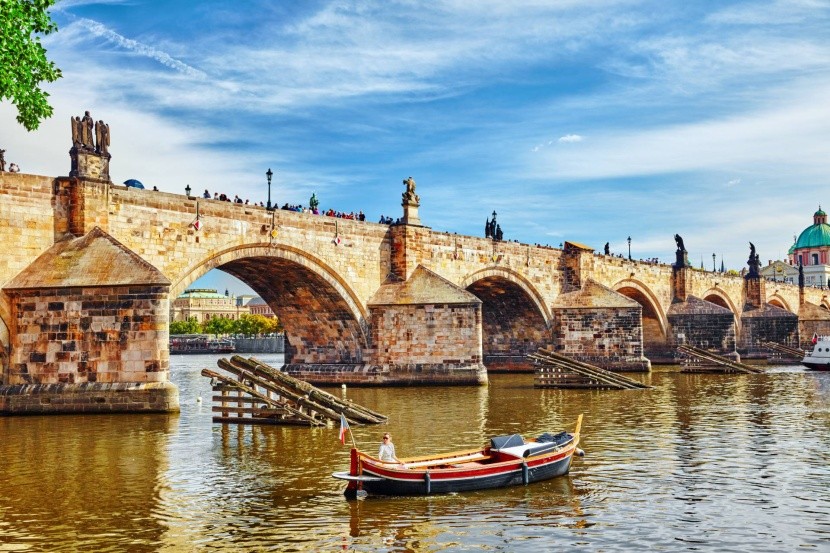
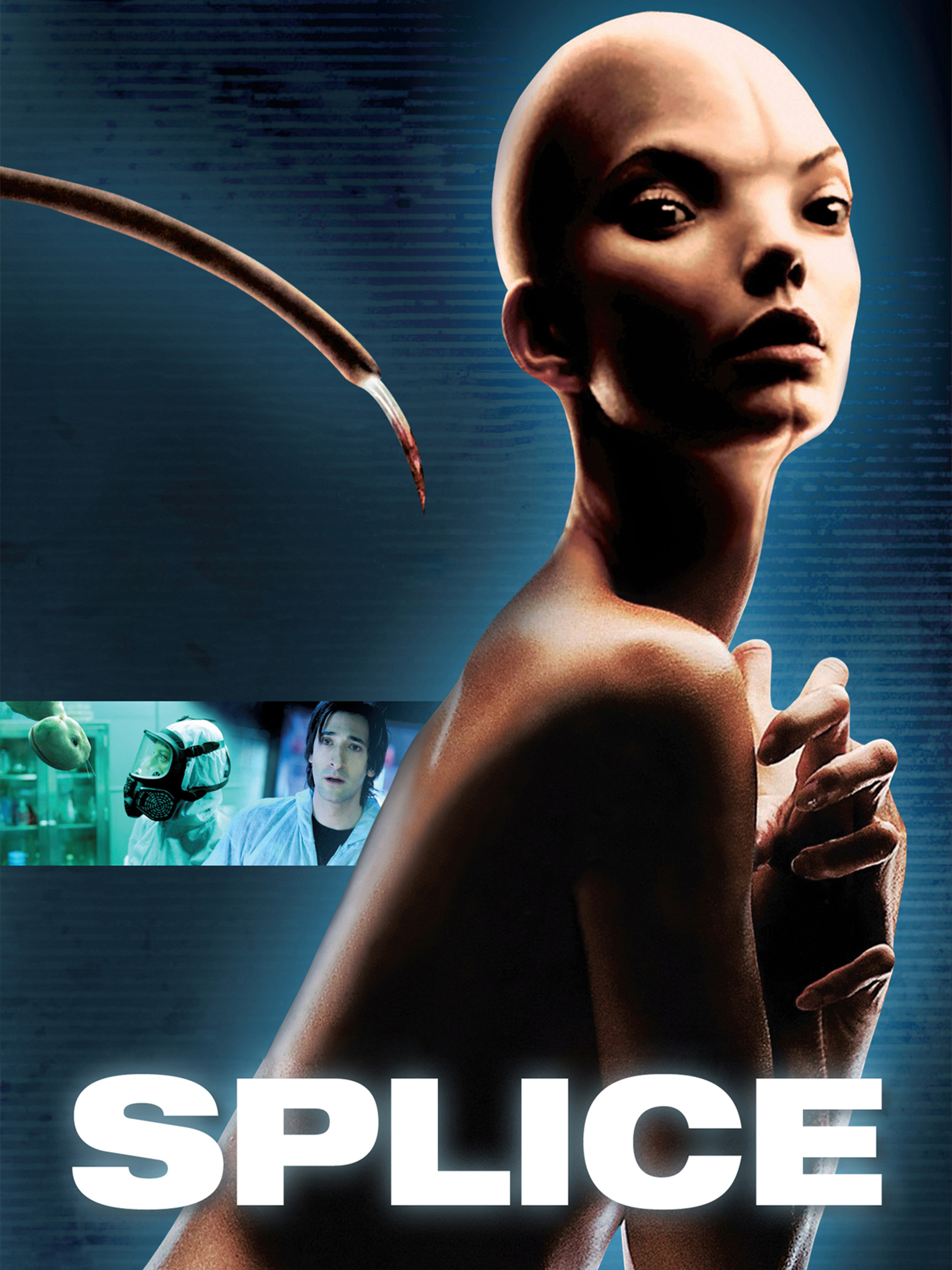
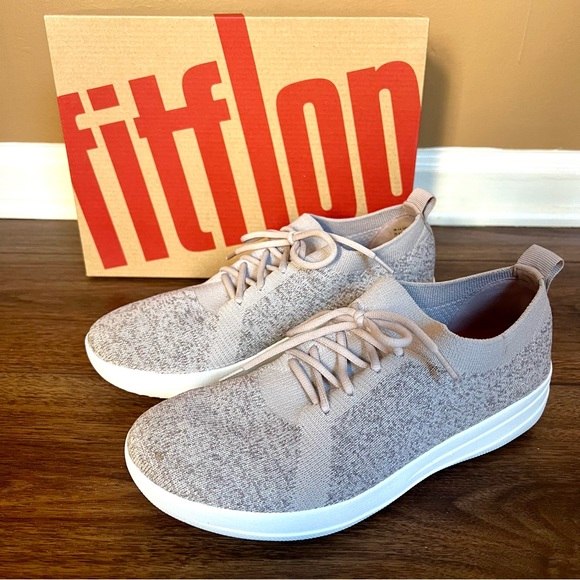
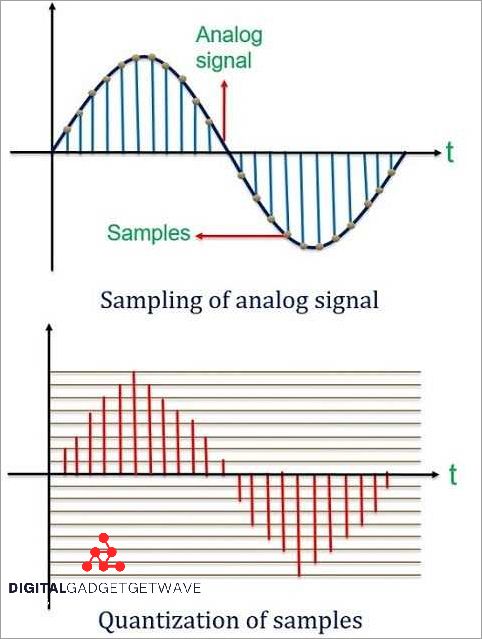
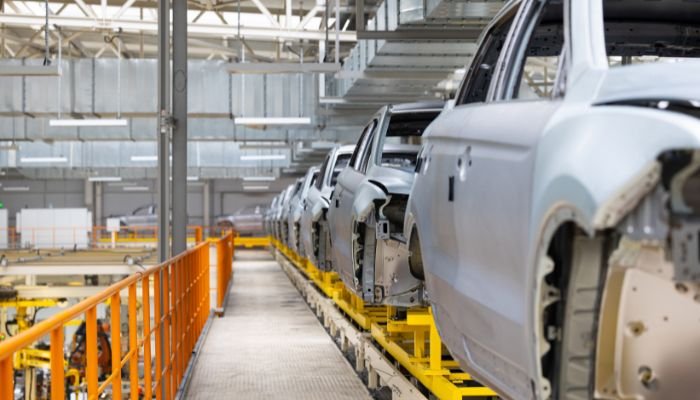